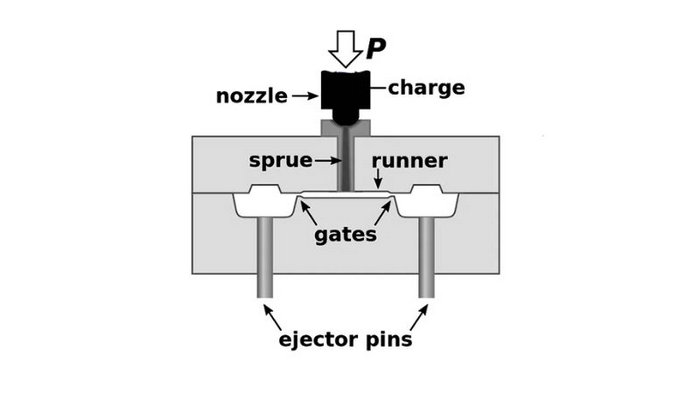
Le moulage par injection, c'est comme gérer une chaîne de montage vraiment cool en miniature, et les éjecteurs sont vos minuscules collègues qui garantissent que chaque pièce sort correctement. Ces épingles sont des éléments clés, souvent négligés, mais elles font le gros du travail lorsqu'il s'agit de sortir vos pièces fraîchement moulées de leurs moules de confinement. Imaginez fabriquer une pièce en plastique parfaite : vos éjecteurs garantissent qu'elle sort dans le monde sans accroc. Ils repoussent la pièce une fois refroidie, ce qui signifie moins de tracas pour vous et un passage plus rapide de la conception au produit réel.
Choisir les bonnes broches d'éjection est crucial car elles doivent correspondre au design et au type de votre produit. Ils se présentent sous différentes formes et tailles, chacun ayant un talent particulier pour traiter des surfaces ou des formes de pièces spécifiques. Considérez vos broches d'éjection comme des aides personnalisables ; vous les choisissez et les positionnez dans le moule afin qu’ils appliquent juste la bonne force. De cette façon, ils ne laissent pas de traces et n’endommagent pas ce que vous avez réalisé.
Points clés à retenir
1. Que sont les éjecteurs et à quoi servent-ils ?
Les broches d'éjection font partie du système d'éjection qui pousse la pièce en plastique refroidie et durcie hors du moule après le processus de moulage par injection. Cela permet le retrait et l’éjection efficaces des pièces moulées.
Le mouliste consacre beaucoup de temps et d’efforts à l’usinage et au polissage des cavités du moule pour garantir des pièces en plastique de haute qualité. Cependant, des éjecteurs de mauvaise qualité peuvent annuler ce travail et endommager le moule en cas de défaillance.
2. Quelle est la broche centrale ?
Une broche centrale est un composant clé utilisé dans les moules d'injection et les moules de moulage sous pression pour créer des caractéristiques internes et des trous dans les pièces moulées ou coulées.
3. Quels sont les types de systèmes d'éjection ?
- Les systèmes d'éjection de plaques utilisent une plaque pour expulser les pièces
- L'éjection d'air souffle de l'air pour éjecter les pièces, idéal pour les pièces fines
- Les broches d'éjection poussent directement sur la pièce pour l'éjecter
4. Que faut-il prendre en compte lors du positionnement des éjecteurs ?
- Les broches doivent pousser sur des surfaces offrant suffisamment de surface pour éjecter la pièce.
- Il faudra peut-être ajouter des tampons éjecteurs si la surface est limitée
- Le placement des broches doit minimiser les marques visibles sur la pièce finale
5. Quels problèmes peuvent survenir avec les éjecteurs ?
- Peut laisser des traces sur la pièce moulée
- Peut ne pas se rétracter complètement en raison d'une résistance ou d'un grippage
- Peut endommager ou rayer les pièces moulées si elles ne sont pas correctement alignées
Considérations de conception pour les broches d'éjection
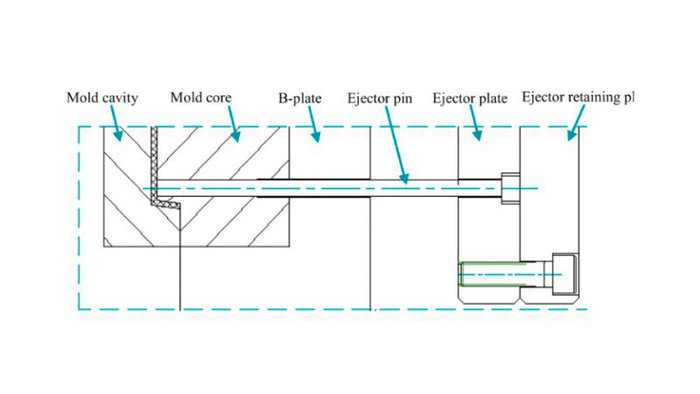
Lorsque vous configurez votre projet de moulage par injection, il est crucial de bien définir la conception de la broche d'éjection. Non seulement ils aident à éjecter la pièce du moule, mais ils jouent également un rôle important dans la qualité finale de vos produits.
Conception du moule et placement des broches
Vous devez vous concentrer sur la conception du moule. Vos broches d'éjection doivent être réparties uniformément sur la pièce pour éviter toute distorsion lors de l'éjection. Assurez-vous qu'il y a une distance suffisante entre les trous des broches d'éjection et les autres éléments du moule pour éviter tout incident.
- Placement des broches d'éjection : visez des positions stratégiques des broches qui soutiennent bien la pièce du moule.
- Ventilation : une ventilation adéquate est essentielle pour éviter la formation de vide qui pourrait perturber l'éjection des pièces.
Taille, position et angles de dépouille
La taille compte ici. Vous ne voulez pas que vos broches soient trop petites pour ne pas pouvoir éjecter la pièce, ou si grosses qu'elles l'endommagent. La position correcte garantit une éjection en douceur, et l'ajout d'angles de dépouille à la conception de la pièce rendra cela encore plus facile.
- Taille : utilisez des épingles plus grandes pour les pièces volumineuses, mais n'allez pas trop loin.
- Position : Alignez les broches avec les sections plus épaisses de la pièce pour une éjection efficace.
- Dépouille : assurez-vous que votre pièce a un angle de dépouille pour une éjection plus facile et moins d'usure sur vos broches.
Matériaux et traitement thermique
Vos broches d'éjection doivent être résistantes. Habituellement, les broches d'éjection ultra-dures sont choisies pour leur durabilité, mais pour les matériaux plus abrasifs et à haute température, les broches d'éjection noires peuvent être votre choix. Le traitement thermique est un gros problème : il renforce les broches afin qu'elles puissent faire leur travail encore et encore sans se plier ni se casser.
Types de broches d'éjection et leurs utilisations
Dans le domaine du moulage par injection, les éjecteurs sont comme vos héros méconnus, démoulant des pièces de manière rapide et fiable. Décomposons les types que vous utiliserez le plus souvent.
Broches d'éjection standard
Les broches d'éjection standard sont votre référence pour la majorité des projets. Ils sont fabriqués en acier durable traité thermiquement qui peut supporter une chaleur jusqu'à 200°C, ce qui leur confère une dureté constante. Considérez ces épingles comme des outils polyvalents et robustes dans votre boîte à outils.
- Matériaux : généralement en acier trempé à cœur
- Résistance à la chaleur : jusqu'à 200°C
- Applications : Éjection plastique générale
Options de lame et de manchon
Le passage à des équipements plus spécialisés, des options de lames et de manchons vous offrent de la flexibilité. Les broches d'éjection de lame ont une forme fine et plate, idéale pour éjecter des pièces à parois fines ou à caractéristiques complexes sans laisser de marques.
Les manchons d'éjection, en revanche, vous offrent un ajustement parfait pour les éjecteurs cylindriques ou ronds. Ils enveloppent les broches, ajoutant une couche supplémentaire de guidage et de support lors de l'éjection de la pièce.
- Broches d'éjection de lame :
- Forme : Profil fin et plat
- Idéal pour : Pièces délicates avec des marques d'éjection minimes
- Manchons d'éjection :
- Fonction : Ajouter un support aux broches d'éjection
- Idéal pour : éjecteurs cylindriques ou ronds
Chaque type d'éjecteur joue un rôle spécifique pour garantir que vos pièces moulées sortent proprement et avec précision. N'oubliez pas que choisir la bonne broche pour le bon travail est la clé d'une opération de moulage en douceur.
Comprendre le processus d'éjection
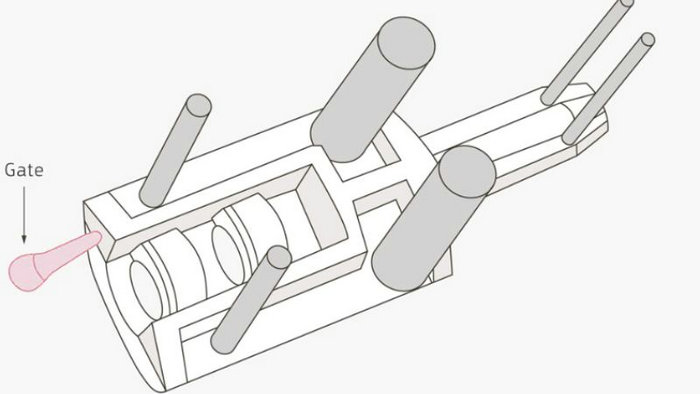
Le processus d’éjection dans le moulage par injection est une question de précision et de timing. Faites les choses correctement et vos pièces ressortent proprement à chaque fois.
Mécanique d'éjection
Votre système d’éjection se met en marche une fois la pièce moulée refroidie. Voici comment cela se déroule :
- Activation de la plaque d'éjection : lorsque le moule s'ouvre, une plaque d'éjection qui maintient les broches d'éjection avance.
- Mécanisme de poussée : les broches poussent uniformément contre la pièce en utilisant une force calculée juste suffisante pour éjecter la pièce sans dommage.
- Post-éjection : le moule se ferme et les broches se rétractent dans leur position d'origine, préparées pour le cycle suivant.
Points à retenir :
- Un contact de surface égale est essentiel pour éviter la déformation de la pièce.
- Les barrières à poteaux peuvent avoir un impact sur la répartition de la force et doivent être prises en compte lors du placement des broches.
Optimiser pour l'efficacité
Pour réduire votre temps de cycle et améliorer la qualité, vous vous concentrerez sur :
- Équilibre d'éjection : répartissez la force pour que la pièce sorte en douceur sans coller ni se déformer.
- Maintenance du système : des contrôles réguliers de votre système d'éjection évitent les temps d'arrêt inattendus. Gardez un œil sur ces épingles et ces tampons !
Problèmes courants et solutions
Lorsqu'il s'agit de moulage par injection, les éjecteurs jouent un rôle essentiel, mais les problèmes de marques d'éjecteurs et d'usure peuvent affecter la qualité et la longévité de vos produits et de vos moules. Voyons comment vous pouvez répondre à ces préoccupations courantes.
Marques d'éjecteur et défauts de surface
Les marques d'éjecteurs sont ces petites imperfections que vous pourriez trouver sur la surface de vos pièces en plastique après le moulage. Ceux-ci sont souvent dus à des broches poussant la pièce hors du moule. Pour minimiser ces défauts inesthétiques, vous devez :
- Choisissez la bonne résine : Certaines résines, en raison de leurs propriétés, sont plus susceptibles que d’autres de présenter des marques d’éjecteurs. Optez pour des résines qui résistent mieux au processus d’éjection.
- Repensez l'emplacement des portes : la position des portes peut influencer l'endroit où la contrainte est appliquée lors de l'éjection. En optimisant l'emplacement des portes, vous pouvez réduire le risque de marques d'épingles.
- Ajustements de conception : de petits ajustements dans la conception de votre produit peuvent faire une grande différence. L'ajout d'angles de dépouille et la prise en compte de l'écoulement et du refroidissement de la résine pourraient éviter les marques d'éjecteurs.
Réduire l'usure
Vos éjecteurs et moules subissent beaucoup de contraintes à chaque cycle d’injection. Pour les protéger de l’usure et assurer le bon fonctionnement de vos opérations :
- Entretien régulier : Gardez un œil sur vos éjecteurs et remplacez-les lorsqu'ils montrent des signes de dommages. Cela évite non seulement les défauts, mais prolonge également la durée de vie de votre moule.
- Sélection du matériau : le matériau de vos éjecteurs est important. Investir dans des broches durables et de haute qualité peut résister aux rigueurs des forces d’éjection et résister à l’usure.
- Polissage et lubrification : gardez vos broches polies et bien lubrifiées pour réduire la friction, ce qui peut entraîner une usure et des dommages prématurés.
Concepts avancés dans la conception des broches d'éjection
Lorsque vous cherchez à optimiser votre processus de moulage par injection, il est crucial de comprendre la conception avancée des broches d'éjection. Les avancées de conception appropriées peuvent améliorer considérablement les performances et la longévité de vos éjecteurs et, par conséquent, l'efficacité de votre moule.
Utilisation du DLC dans les broches d'éjection
Les revêtements en carbone de type diamant (DLC) ont révolutionné la conception des broches d'éjection en réduisant l'usure et la friction. Imaginez un scénario dans lequel votre éjecteur doit glisser à travers le canal de l'éjecteur en douceur, encore et encore ; Les revêtements DLC garantissent que vos mouvements sont fluides avec une résistance minimale. Ceci est particulièrement avantageux lorsque vos broches s'interfacent avec une porte de bord ou lors de l'éjection de pièces avec des angles de dépouille serrés.
Avantages clés:
- Frottement réduit
- Résistance accrue à l’usure
- Compatible avec divers métaux, y compris les broches d'éjection en nitrure H13
Précision et personnalisation
La personnalisation des éjecteurs en fonction des besoins spécifiques de votre projet de moulage n'est pas seulement une question de précision : il s'agit également d'obtenir l'ajustement parfait pour des résultats optimaux. Qu'il s'agisse d'un tampon d'éjection surélevé pour une répartition plus uniforme de la force ou du réglage du système de canaux pour un débit efficace, l'accent mis sur la précision garantit que chaque aspect de votre système d'éjection est adapté à la conception de votre pièce.
- Fabrication de précision : assure un alignement parfait dans le canal de l'éjecteur, ce qui est essentiel pour un fonctionnement fluide.
- Options de personnalisation : incluez des considérations spécifiques pour diverses caractéristiques du moule, telles que la conception de tampons d'éjection surélevés ou la modification des angles de dépouille pour faciliter le démoulage des pièces.