Das Herz von Spritzguss liegt der Formkern, eine kritische Komponente, die die inneren Merkmale des geformten Produkts prägt. Das Verständnis der wesentlichen Bestandteile von Spritzgusskernen ist für die Optimierung von Produktdesign und -qualität von entscheidender Bedeutung.
Dieser Artikel befasst sich mit den grundlegenden Aspekten von Formkernen und untersucht, wie sie den Herstellungsprozess und die Leistung des Endprodukts beeinflussen. Durch die Untersuchung wichtiger Aspekte wie Materialauswahl und Designstrategien möchten wir Ingenieuren und Herstellern, die ihre Best Practices im Spritzgussverfahren umsetzen möchten, wertvolle Einblicke bieten.
Lassen Sie uns zunächst den grundlegenden Prozess des Spritzgießens vorstellen.
Der grundlegende Prozess des Spritzgießens umfasst mehrere wichtige Schritte, bei denen Kunststoffmaterialien in fertige Produkte umgewandelt werden. Hier ist eine vereinfachte Übersicht:
- Klemmung: Der Prozess beginnt mit dem Schließen der Form, die normalerweise aus zwei Hälften besteht. Diese Hälften werden zur Vorbereitung des Einspritzens fest zusammengeklemmt.
- Injektion: Kunststoffgranulat oder -pellets werden in einen beheizten Zylinder gefüllt, wo sie schmelzen. Der geschmolzene Kunststoff wird dann durch eine Düse in den Formhohlraum gespritzt und füllt den Raum vollständig aus.
- Wohnung: Durch Druck wird sichergestellt, dass der geschmolzene Kunststoff alle Teile der Formhöhle ausfüllt und das Produkt dem Design der Form entspricht.
- Kühlung: Die Form wird abkühlen gelassen, sodass der Kunststoff in der Formhöhle erstarren kann.
- Formöffnung: Nach dem Abkühlen werden die Formhälften geöffnet, um das erstarrte Teil freizugeben.
- Auswurf: Auswerferstifte oder andere Mechanismen drücken das fertige Teil aus der Form, bereit für die weitere Verarbeitung oder Verpackung.
Was ist ein Spritzgusskern?
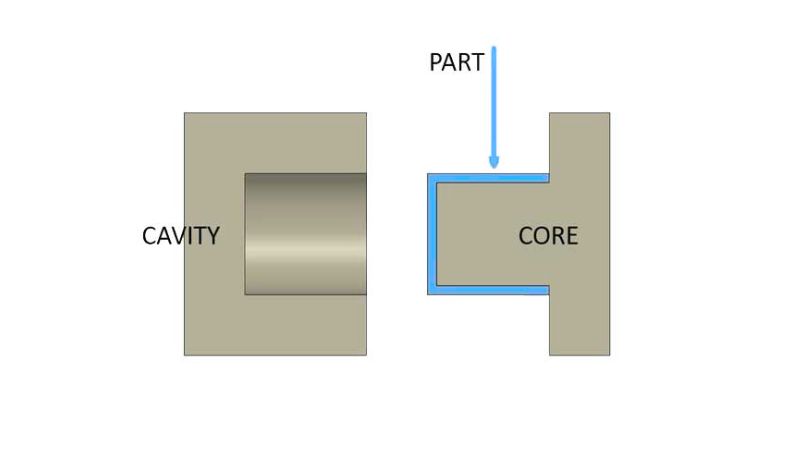
Der Spritzgusskern ist ein festes oder bewegliches Bauteil innerhalb der Form, das die inneren Merkmale oder Hohlräume des endgültigen Formteils bildet. Er stellt die Form und Geometrie der gewünschten inneren Merkmale des Teils dar, wie z. B. Hohlräume oder komplexe innere Strukturen.
Was ist der Unterschied zwischen Hohlraum und Kern in einer Form?
Als Kern ist die Kavität ein weiteres wichtiges Formbauteil beim Kunststoffspritzguss, das oft auf eine Oberfläche poliert wird, die der gewünschten endgültigen Oberflächenbeschaffenheit des Teils entspricht. Gemeinsam formen sie das endgültige Formteil.
Der Kern formt die inneren Merkmale, während die Kavität die äußeren Merkmale des Teils formt.
Dabei befindet sich der Formkern in der beweglichen Hälfte (B-Seite), die häufig am Auswerfervorgang beteiligt ist, und die Kavität befindet sich in der festen Hälfte (A-Seite), wobei die Kavität weniger direkt beteiligt ist.
Wie wird der Spritzgusskern hergestellt?
Das richtige Material auswählen
Materialauswahl denn der Kern ist zwingend erforderlich, da er den hohen Temperaturen und Drücken des geschmolzenen Kunststoffs standhalten muss, ohne sich zu verformen.
Die Leistung des Kerns beeinflusst nicht nur die Qualität, sondern auch die Effizienz des Spritzgussverfahrens, wodurch Teile entstehen, die strenge Spezifikationen erfüllen.
- Stahl: Hochwertiger Stahl ist aufgrund seiner Haltbarkeit und Verschleißfestigkeit eine beliebte Wahl, was ihn ideal für die Produktion großer Stückzahlen macht. Dazu gehören Typen wie Edelstahl, P20 und H13.
- Aluminium: Aluminium ist für sein geringes Gewicht und seine schnelleren Heiz- und Abkühleigenschaften bekannt und wird häufig für Prototypwerkzeuge oder die Produktion kleiner Stückzahlen verwendet.
- Beryllium-Kupfer-Legierungen: Wird in Bereichen der Form verwendet, in denen eine schnelle Wärmeabfuhr erforderlich ist, oder in Teilen der Form mit komplizierter Geometrie.
- Vorgehärteter Stahl: Eine kostengünstige Option für weniger anspruchsvolle Anwendungen; keine zusätzliche Wärmebehandlung erforderlich.
- Werkzeugstahl: Für Anwendungen mit hohem Verschleiß werden Werkzeugstähle wie D2 oder A2 verwendet, die Robustheit und Langlebigkeit bieten.
Herstellungsprozess und Präzision
Moderne Bearbeitungstechniken wie CNC-Fräsen und elektrische Entladungsbearbeitung (EDM) tragen wesentlich dazu bei, die für die Kerne erforderliche hohe Präzision zu erreichen.
- CNC-Fräsen: Bietet Genauigkeit durch computergesteuerte Bearbeitung.
- Funkenerosion: Wird für komplizierte Details und komplexe Geometrien verwendet.
Welchen Einfluss hat der Formkern auf die Produktqualität?
Schwankungen in der Kern- und Formqualität beim Spritzgießen können auf mehrere Faktoren zurückgeführt werden, die sich auf die Leistung und Konsistenz der Formteile auswirken:
Ursache | Beschreibung |
Kernverschiebung | Fehlausrichtung des Formkerns während des Einspritzens, was zu Maßungenauigkeiten führt. |
Kleben | Der Kern bleibt beim Auswerfen im Teil stecken, häufig aufgrund unzureichender Entformungsschrägen oder übermäßiger Reibung. |
Verziehen | Maßverzerrungen entstehen durch die Verformung des Kerns unter hohen Temperaturen und Druckzyklen. |
Rissbildung oder Bruch | Kernschäden sind auf Spannungen und Druck zurückzuführen, die häufig durch die Verwendung weniger haltbarer Materialien verursacht werden. |
Verschleiß | Abrieb und Erosion durch Dauergebrauch führen zu einer Verschlechterung der Oberflächenqualität und Maßhaltigkeit. |
Kühlungsprobleme | Eine unzureichende Kühlung oder Wärmeübertragung führt zu längeren Zykluszeiten und kann zu Verformungen oder Maßänderungen führen. |
Entlüftungsprobleme | Durch die unzureichende Entlüftung werden Luft und Gase eingeschlossen, was zu Oberflächenfehlern, Hohlräumen oder einer unvollständigen Teilefüllung führt. |
Material- und Designvariabilität | Variabilität der Materialeigenschaften und Designkomplexität wirken sich auf Lebensdauer und Leistung der Form aus. |
Wartungsherausforderungen | Mangelnde regelmäßige Wartung führt zu Problemen wie Korrosion, Verunreinigung oder Verschleiß und beeinträchtigt somit die Leistung der Form und die Produktqualität. |
Was ist der Entformungswinkel?
Der im vorherigen Abschnitt erwähnte Entformungswinkel bezieht sich auf eine leichte Verjüngung, die beim Spritzgießen auf die vertikalen Oberflächen eines Teils angewendet wird. Diese Verjüngung trägt dazu bei, dass das Teil leicht aus der Form gelöst werden kann, ohne dass es dabei zu Beschädigungen kommt.
Normalerweise wird für die meisten Teile ein Entformungswinkel von 1 bis 2 Grad empfohlen. Bei tieferen oder strukturierten Oberflächen ist eine größere Entformungsschräge erforderlich.
Es gibt positive und negative Entformungsschrägen. Eine positive Entformungsschräge bedeutet, dass der Winkel größer als der Referenzwinkel ist, was die Teilefreigabe erleichtert. Eine negative Entformungsschräge kann die Formkonstruktion erschweren, da die Form zur Teileentnahme möglicherweise in mehrere Teile zerlegt werden muss.
Wie wählt man die Kern- und Hohlraumplatzierung beim Spritzgießen?
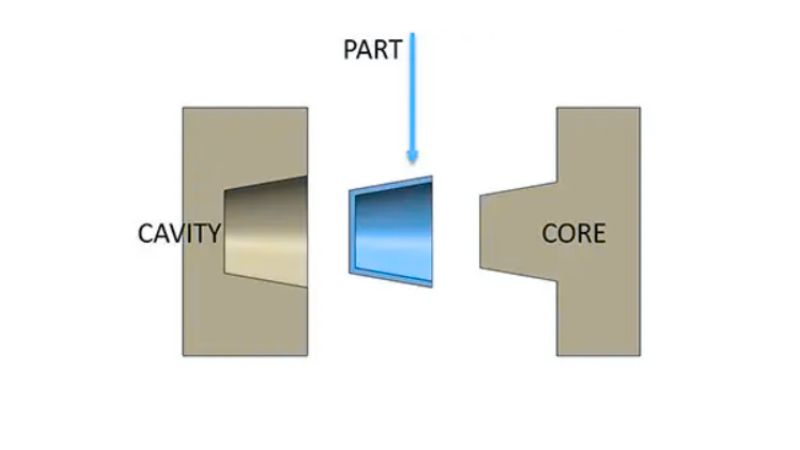
Welche Faktoren beeinflussen die Platzierung von Kern und Hohlraum?
Die Platzierung von Kern und Hohlraum beim Spritzgießen wird von mehreren Schlüsselfaktoren beeinflusst:
Teiledesign
Die Komplexität und Geometrie des Teils, einschließlich Merkmalen wie Löchern und Vertiefungen, bestimmen die Platzierung von Kern und Hohlraum. Hervorstehende Merkmale erfordern normalerweise Kerne, während vertiefte Merkmale durch Hohlräume gebildet werden.
Materialeigenschaften
Die Anordnung von Kern und Hohlraum in einer Form wird durch die Schrumpfrate, die Fließeigenschaften und die Einspritzgeschwindigkeit des Materials beeinflusst. Wenn ein Material eine niedrige Schrumpfrate aufweist, kann es schwierig sein, sicherzustellen, dass das Teil auf der Seite mit den Auswerferstiften bleibt, was spezielle Designanpassungen erfordert.
Da die meisten Kunststoffe erheblich schrumpfen, ist es wichtig zu verstehen, welchen Einfluss die Materialeigenschaften auf die Platzierung von Kern und Hohlraum haben können.
Layout des Auswurfsystems
Nach der Abkühlphase muss beim Öffnen der Form das Spritzgussteil immer an der Seite mit den Auswerferstiften hängen bleiben.
Das Design und die Form des Auswerfersystems beeinflussen die Platzierung des Kerns und der Kavität, um ein gleichmäßiges und zuverlässiges Auswerfen des Teils zu gewährleisten.
Symmetrie und Gate-Standort
Der Anguss ist der Hauptkanal, der geschmolzenen Kunststoff von der Spritzgussmaschine in die Form leitet. Normalerweise läuft er direkt in die Form, manchmal kann er aber auch direkt in die Formhöhle fließen. In diesem Fall spricht man von einem direkten Anguss.
Angusskanäle sind kleinere Kanäle, die vom Anguss abzweigen, um den geschmolzenen Kunststoff in verschiedene Teile der Form zu verteilen. Mit diesem Aufbau können mehrere Teile gleichzeitig hergestellt werden, was insbesondere bei kleinen Artikeln kostengünstig ist.
Angussöffnungen sind die kleinen Öffnungen, durch die der Kunststoff von den Angusskanälen in die Formhöhle gelangt. Sie sind schmaler als die Angusskanäle und helfen dabei, den Kunststofffluss in die Form zu kontrollieren.