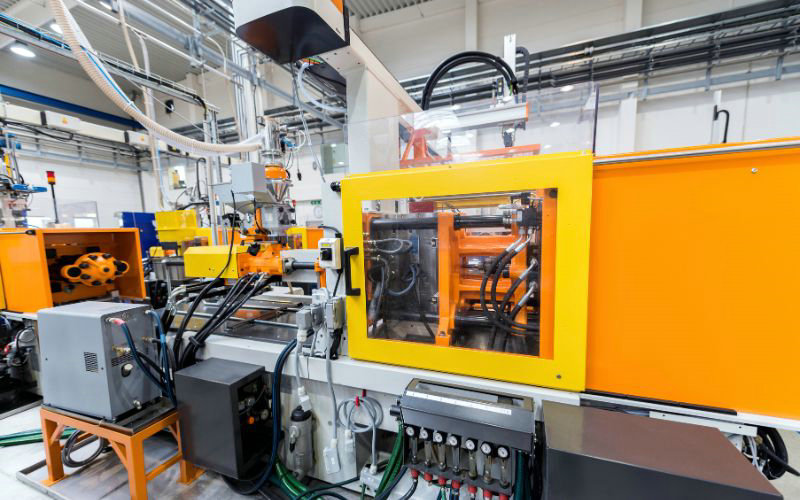
Conception du système de refroidissement du moule par injection
Le système de refroidissement assure un refroidissement uniforme et un contrôle efficace de la température lors de la conception de votre moule d'injection. Cela a non seulement un impact sur la qualité de la pièce moulée, mais influence également de manière significative le temps de cycle et l'efficacité du refroidissement. Les chicanes, les barboteurs et les broches thermiques sont des stratégies de refroidissement spécialisées utilisées pour optimiser la répartition de la température dans les moules à injection, en particulier dans les zones difficiles que les canaux percés ordinaires ne peuvent pas atteindre efficacement. Ils améliorent l'évacuation de la chaleur en augmentant la surface de contact avec le liquide de refroidissement ou en utilisant un transfert de chaleur à changement de phase. Une conception appropriée de ces fonctionnalités est essentielle pour obtenir un refroidissement uniforme des pièces et minimiser les temps de cycle. Examinons maintenant leurs fonctions uniques :
Chicanes
- Un déflecteur est un canal de refroidissement percé perpendiculairement à une conduite de refroidissement principale, doté d'une lame qui sépare le canal en deux passages semi-circulaires.
- Le liquide de refroidissement s'écoule d'un côté de la lame depuis la conduite principale, tourne autour de la pointe de l'autre côté, puis retourne vers la conduite principale.
- Les chicanes augmentent la surface que le liquide de refroidissement peut atteindre dans les zones qui manqueraient normalement de refroidissement.
- La tôle formant le déflecteur peut être tordue en forme d'hélice pour des diamètres de 12 à 50 mm afin de fournir une répartition plus homogène de la température.
- Les noyaux en spirale à simple ou double vol constituent un autre développement des déflecteurs.
Barboteurs
- Un barboteur s'apparente à un déflecteur mais remplace la lame par un petit tube.
- Le liquide de refroidissement s'écoule dans le bas du tube et « fait des bulles » vers le haut, puis s'écoule autour de l'extérieur du tube jusqu'au canal principal.
- Les barboteurs offrent le refroidissement le plus efficace pour les noyaux minces.
- Les diamètres intérieur et extérieur du barboteur doivent avoir un rapport de 0,707 pour une résistance à l'écoulement égale.
- Les barboteurs peuvent également être utilisés pour refroidir les sections de moules plates qui ne peuvent pas accueillir de canaux percés.
Broches thermiques
- Une broche thermique est une alternative aux déflecteurs et aux barboteurs constitués d'un cylindre scellé rempli de fluide.
- Le fluide se vaporise en extrayant la chaleur du moule et se condense en libérant continuellement la chaleur au liquide de refroidissement.
- Les broches thermiques ont une efficacité de transfert de chaleur près de 10 fois supérieure à celle des inserts en cuivre ou en alliage de cuivre.
- Les espaces d'air entre la broche thermique et le moule doivent être évités ou remplis d'un mastic hautement conducteur pour une conduction thermique optimale.
Différents types de systèmes de refroidissement pour moules à injection
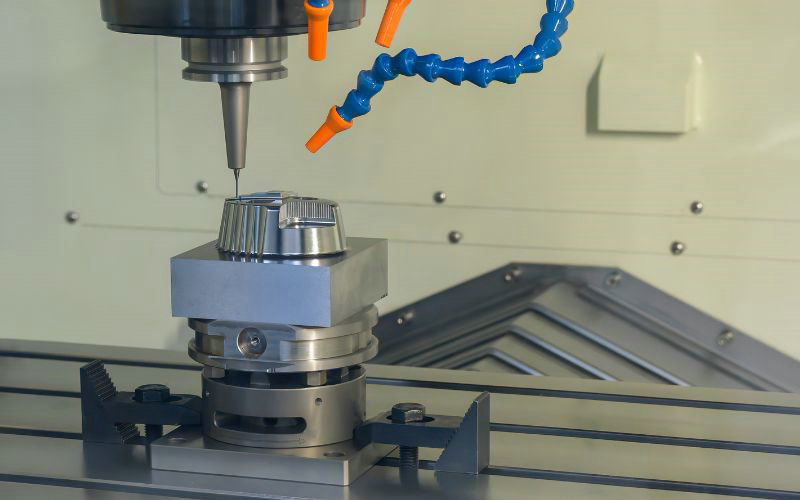
Le bon système de refroidissement assure une répartition uniforme de la température, minimise la déformation et le retrait et favorise l’efficacité énergétique et l’efficacité du refroidissement.
Systèmes refroidis à l'eau
Les systèmes refroidis par eau sont la méthode de refroidissement la plus couramment utilisée dans le moulage par injection en raison de leur efficacité et de leur efficacité en matière d'évacuation de la chaleur. Ces systèmes font circuler l'eau réfrigérée à travers des canaux à l'intérieur du moule, absorbant la chaleur du moule et du plastique fondu. Cette méthode est particulièrement efficace pour les moules complexes et les matériaux sensibles à la température, car elle offre d'excellentes capacités de contrôle de la température et d'absorption de la chaleur.
Systèmes refroidis par air
Les systèmes refroidis par air utilisent des ventilateurs ou des soufflantes pour dissiper la chaleur de la surface du moule par convection. Cette méthode est plus simple et moins coûteuse à mettre en œuvre que les systèmes refroidis par eau. Le refroidissement par air convient aux conceptions de moules moins complexes et aux matériaux moins sensibles aux fluctuations de température. Cependant, il est moins efficace en termes d’absorption de chaleur et de contrôle de la température que les systèmes refroidis par eau.
Systèmes refroidis à l'huile
Les systèmes refroidis par huile sont utilisés dans les scénarios où un refroidissement très rapide est requis. Ces systèmes font circuler de l’huile, qui peut évacuer la chaleur plus efficacement que l’air. Le refroidissement à l'huile est généralement plus coûteux que le refroidissement à l'eau ou à l'air, mais il est privilégié dans les grandes opérations de moulage par injection ou pour les matériaux nécessitant une transition très rapide des températures élevées aux températures basses.
Systèmes de refroidissement cryogéniques
Les systèmes de refroidissement cryogénique utilisent des substances à température extrêmement basse, comme l'azote liquide, pour refroidir rapidement le moule. Cette méthode avancée peut réduire considérablement le temps de refroidissement et la consommation d'énergie, mais est généralement réservée aux applications spécialisées en raison de la complexité et des coûts impliqués.
Systèmes de refroidissement à supports mixtes
Pour personnaliser la gestion thermique, vous pouvez rencontrer des systèmes de refroidissement mixtes qui mélangent différents fluides de refroidissement, tels que l'air et l'eau. Ces systèmes hybrides visent à tirer parti des avantages de chaque support, comme le refroidissement rapide de l'eau avec la simplicité des systèmes à air, optimisant ainsi l'efficacité pour des applications spécifiques de moulage par injection.
L'impact du refroidissement des moules par injection sur les produits moulés

La phase de refroidissement dans le processus de moulage par injection joue un rôle crucial dans la détermination de la qualité, de l'efficacité et du succès global des produits moulés. Cette phase a un impact direct sur divers aspects du produit final, notamment le cycle de moulage, les modalités, la précision dimensionnelle et les propriétés mécaniques.
Cycle de moulage
Le temps de refroidissement représente une partie importante du cycle de moulage par injection, représentant environ 50% à 80% de la durée totale du cycle. Un refroidissement efficace est essentiel pour réduire la durée du cycle de moulage, augmentant ainsi l’efficacité et le rendement de la production. Un système de refroidissement bien conçu peut réduire considérablement le temps de refroidissement sans compromettre la qualité du produit moulé, ce qui entraîne des cadences de production plus rapides et des coûts de fabrication inférieurs.
Modalité
La modalité d'un produit moulé fait référence à ses caractéristiques physiques et esthétiques, notamment la finition de surface, le gauchissement et la présence de défauts tels que des marques d'évier ou des lignes de soudure. La phase de refroidissement influence ces caractéristiques en affectant la façon dont le matériau se solidifie dans le moule. Un refroidissement uniforme et contrôlé peut prévenir les défauts et garantir une finition de surface de haute qualité. À l’inverse, un refroidissement irrégulier peut entraîner des déformations et d’autres défauts compromettant l’apparence et la fonctionnalité du produit.
Précision dimensionnelle
La précision dimensionnelle est essentielle pour les performances et l’assemblage des pièces moulées par injection. La phase de refroidissement a un impact direct sur le retrait et le gauchissement du matériau, ce qui affecte à son tour la précision dimensionnelle du produit final. Un refroidissement adéquat garantit un retrait uniforme et minimise le gauchissement, ce qui permet d'obtenir des pièces répondant à des spécifications dimensionnelles précises. Des facteurs tels que la température du moule, la conception des canaux de refroidissement et le fluide de refroidissement peuvent être optimisés pour obtenir la précision dimensionnelle souhaitée.
Propriétés mécaniques
La phase de refroidissement influence également les propriétés mécaniques des produits moulés par injection, telles que la solidité, la rigidité et la résistance aux chocs. Un refroidissement rapide ou irrégulier peut induire des contraintes résiduelles au sein du matériau, réduisant potentiellement sa résistance et augmentant sa susceptibilité à la fissuration ou à la rupture sous charge. Un refroidissement contrôlé peut favoriser une cristallisation uniforme dans les polymères semi-cristallins et minimiser les contraintes résiduelles, améliorant ainsi les propriétés mécaniques du produit final.
En conclusion, la phase de refroidissement dans le moulage par injection est cruciale pour garantir l'efficacité du cycle de moulage, la qualité et les modalités des produits moulés, leur précision dimensionnelle et leurs propriétés mécaniques. Un système de refroidissement bien conçu, adapté aux exigences spécifiques du matériau et de la pièce moulée, est essentiel pour produire des produits moulés par injection de haute qualité qui respectent ou dépassent les normes de performance et d'esthétique.